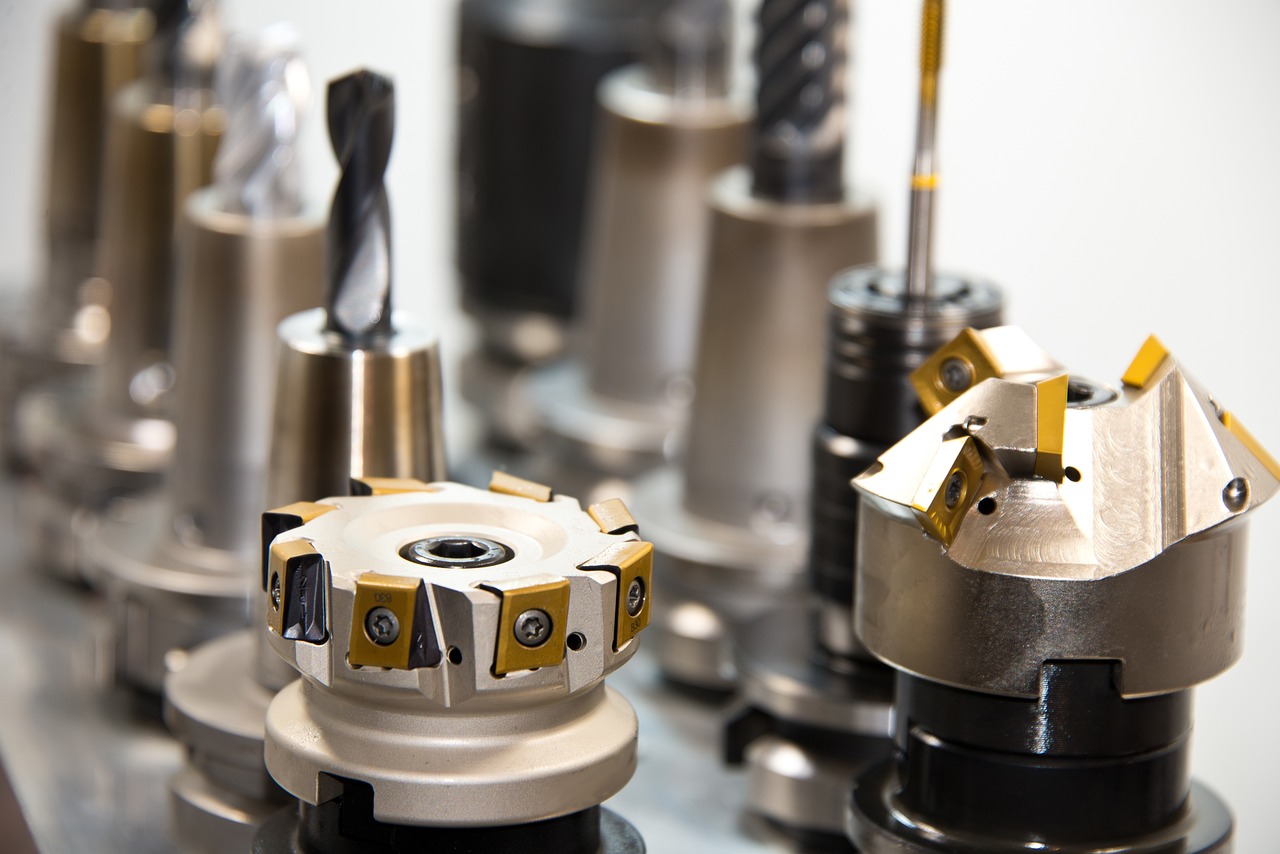
There is an increasing need to juggle becoming more efficient, bridging the skills gap and keeping up with customer needs. The manufacturing industry has witnessed significant technological advancements over the past few decades such as 3d printing, IoT, robotics and augmented reality - and we know that as soon as technology is available there’s always someone working on the next iteration!
For US machine shop owners, embracing technology is crucial for driving growth and ensuring long-term business success. Manufacturers face increasing customer expectations, including shorter lead times, customised products, and impeccable quality.
What I’ve seen is that businesses in the industry are experiencing significant investment and development, driving the demand for computer-aided manufacturing. Computer-aided manufacturing systems have become essential in optimising the manufacturing process as they can reduce errors and improve efficiency.
Traditional manufacturing approaches are struggling to keep up with today's competitive market. It is imperative to leverage technology-driven solutions for sustained growth and to remain in business. Businesses in the manufacturing sector are finding it difficult to onboard new staff or find qualified machinists and technicians. This has resulted in a talent gap that not only hampers productivity and growth.
In recent years the CAM market has experienced significant growth in recent years and the industry needs to ensure that it improves the technology to meet market demands. Automation solutions, robotics, and digital tools enable machine shops to streamline operations, optimise resource allocation, and enhance overall efficiency. Enabling the business to reallocate existing workers to focus on higher-value tasks that require human creativity and problem-solving skills.
CAM software can help automate some of the processes associated with these machines. This doesn’t solve everything. In a factory if a machine sits idle for 8 hours - that’s 8 hours machine shops don’t get back. The average person works only eight hours a day, leaving the CNC machine running idle in the shop - effectively wasting opportunities to earn revenue. Adopting technology doesn’t necessitate the requirement to have people as part of the process - it just reallocates their skills - providing increased job satisfaction over doing those mundane repetitive tasks that they have been sucked into doing to keep things moving.
Improving quality and consistency
Ensuring product quality and consistency is paramount. Technological advancements provide machine shops with advanced quality control mechanisms that surpass traditional inspection methods. Sensors, real-time monitoring, and data analytics enable machine shops to detect defects, identify process variations, and take corrective actions promptly. By implementing digital quality control systems, shops can reduce scrap rates, enhance customer satisfaction, and build a reputation for delivering superior products.
Leveraging technology to improve quality and consistency can also reduce the burden on staff, allowing them to focus on more interesting tasks. When CloudNC developed CAM Assist customers experienced significantly reduced time for CAM-ing a part, thanks to toolpath automation - allowing experts to focus their efforts on where they can make the most difference, improving output across the board.
Enabling innovation and customisation
Technology-driven advancements empower machine shops to explore new possibilities in design, manufacturing, and customisation. Advanced CAD/CAM software, simulation tools, and digital prototyping enable engineers and designers to create complex components with ease, while rapid prototyping and additive manufacturing technologies offer flexibility and speed in product development.
Industries and customers are increasingly demanding more. Compliance with industry standards, regulations, and certifications is essential for staying competitive. Technological advancements enable machine shops to meet these expectations effectively and efficiently. Digital solutions enable machine shops to track and trace materials, maintain comprehensive documentation, and ensure compliance throughout the production process.
The factory of the future
The Factory of the Future represents a comprehensive approach to manufacturing that combines traditional approaches with cutting-edge digital capabilities. By integrating technology across the supply chain and production system, machine shop owners can achieve enhanced flexibility, productivity, and sustainability. Key elements of the Factory of the Future include smart production processes, circular value chains, advanced IT infrastructure, and a safety-oriented culture.
Tailoring the approach to industry-specific needs and ambitions is crucial for success. For example, lights-out manufacturing is an emerging concept that complements the Factory of the Future. Japanese company FANUC established a lights-out factory back in 2001, employing automation technologies to build robots. While lights-out manufacturing is often misunderstood as having zero people onsite, it involves leveraging automation to optimise productivity and minimise human intervention.
Technological Advantage
Embracing technology is paramount for US machine shop owners seeking growth and long-term success. By leveraging CNC technology, automation, and Industry 4.0 solutions, machine shops can overcome workforce limitations, improve efficiency, and enhance product quality. Digital solutions enable sustainable practices, optimise processes, and unlock new levels of productivity.
Here at CloudNC we’re using what we’ve learnt over the last 8 years from our factory to enable solutions such as CAM Assist aim to relieve some of the burdens of the industry and reduce programming time by up to 80%. Read more!