.png)
The inspiration for CloudNC’s existence was my desire to make manufacturing anything as easy as it is to 3D print something.
Fundamentally, I believe that precision machining today is a bottleneck in the manufacturing process that prevents us from making parts and components efficiently and easily - preventing innovation and global economic growth.
Our first software solution, CAM Assist, represents our first steps along the path of making that happen: it autocompletes around 80% of the CNC machine programming process, enabling manufacturers to save time and effort.
At its core CAM Assist is like a machining technician. It has a practical understanding of the physics and processes of cutting metal so it can make the sort of decisions that a machinist would make.
But what’s stopping CAM Assist from doing the whole journey today - and what do the next steps in the journey towards one-click manufacturing look like? Let’s find out.
.png)
3D chess
Today, there is a 3D printer and a laser cutter in the CloudNC office. There are almost no restrictions on what a new employee can make with it - they can essentially design anything, and they could do so without any considerations about optimising the design for manufacture, and the printer will make it with one click (as long as it’s filled it up with resin).
It’s incredibly simple to go from pulling it out of the box to first print. (Going from unboxing to the first component off the laser cutter took less than 5 minutes; the same test for the 3D printer was 1 hour for set up, and another 2 hours for a print to complete.)
In contrast, if that employee were to do that in our factory in Chelmsford with a CNC machine, they would get stuck very very quickly. To start with, the machine interface isn’t intuitive, and requires training. Then, we’ll likely need to make changes to the tooling and workholding, and it’s not easy to change them.
Presuming they can get the right tool for the machine, they then need to go into their CAM package and tell it what size and shape it is, and what the cutting parameters are - which means they need the manufacturer’s handbooks for each tool they’re using. So already, just to set up the machine for one tool, you’re at the point where you require a lot of expertise to know how to do that correctly.
And then if they actually want to make the component they want, they need to program every move effectively by hand, as well as figuring out how they’re going to hold the stock in the machine. Simple things like ‘How am I going to cut the back of the component off’ can be actually quite complex and time consuming to solve.
Let’s assume they get through that stage and have pressed the go button - job done, right? Not at all - they now need to watch the machine make their component (called proving out the program, or proveout for short) as if they’ve made a mistake then they’re going to potentially break an extremely expensive bit of kit - perhaps the cutter, perhaps the machine itself. Ultimately it’s pretty hard to break a 3D printer - but it’s not that hard to crash a CNC machine.
What I would like to be able to happen is to be able to go walk up to the CNC machine and have as much of that process automated as possible. Standard tools are already set up, the software already knows feeds and speeds, and it can already work out how to program most of the machining of a part so there’s just a little bit of tidying up to do. Basically, I want the software to lead me through the journey of making a part as much of the way as possible - really, like 3D printing software does.
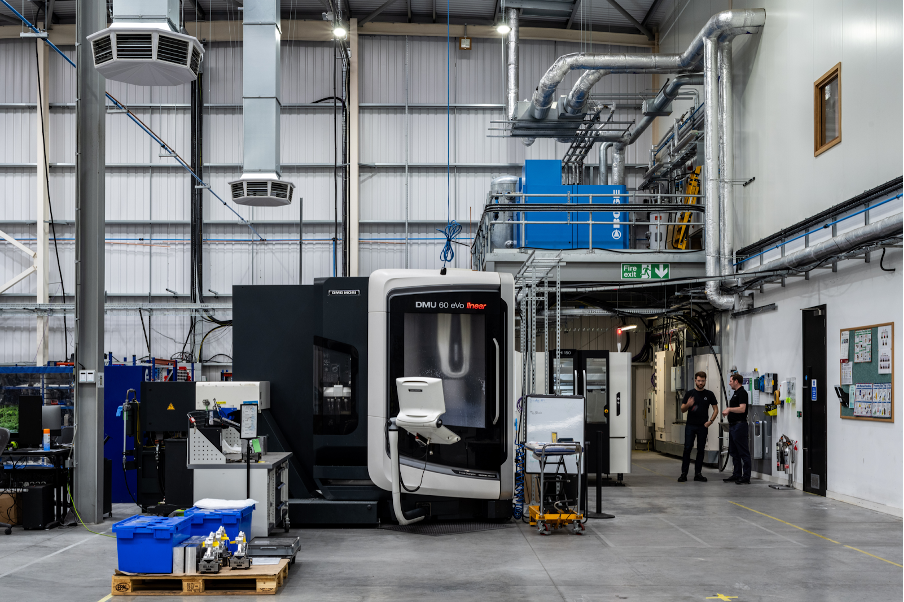
Getting closer
Ideally, of course, the dream would be more all-encompassing - you could have a machine with a couple of hundred tools in it, combined with flexible work holding, and software that knows how to machine almost anything: meaning the set up is automatic (with error-checking built in). That means a lot of the expertise needed today to make the simplest part isn’t required for everything - and brings you closer to the single-click vision.
Now, CAM Assist is the first step on the way to that goal - but there should be no illusions, achieving this in total is several years away at least.
However, I am positive about the possibilities of this being achieved, not least because of our own experience: 8 years ago, when we started making CAM Assist, no-one would have thought we’d have got anywhere close to what our software can do today.
And, of course, on the way to achieving single-click manufacturing - whenever that might be - there’s a huge amount of value we can add along the way that will make it easier and easier for a workshop owner or machinist to manufacture complex parts and components.
For example, in no particular order, future improvements we have in our sights include:
- Positional multi-axis machining
- Complex materials
- Automatic feeds and speeds
- Simplified price estimating
- Simplified fixtures
- Improved design for manufacturing feedback, through your CAM program
- Automated in-process inspection
These are all product developments that could feasibly be added to CAM Assist in the near to medium term - increasing our solution’s utility even further and helping make machining more efficient, and lower touch.
If any of these advances especially excite you - or if there are obvious omissions that you think we should be working on instead that would make a real difference to your operations - let me know: we’d love to get a clearer view of what use case improvements really matter to machinists around the world!