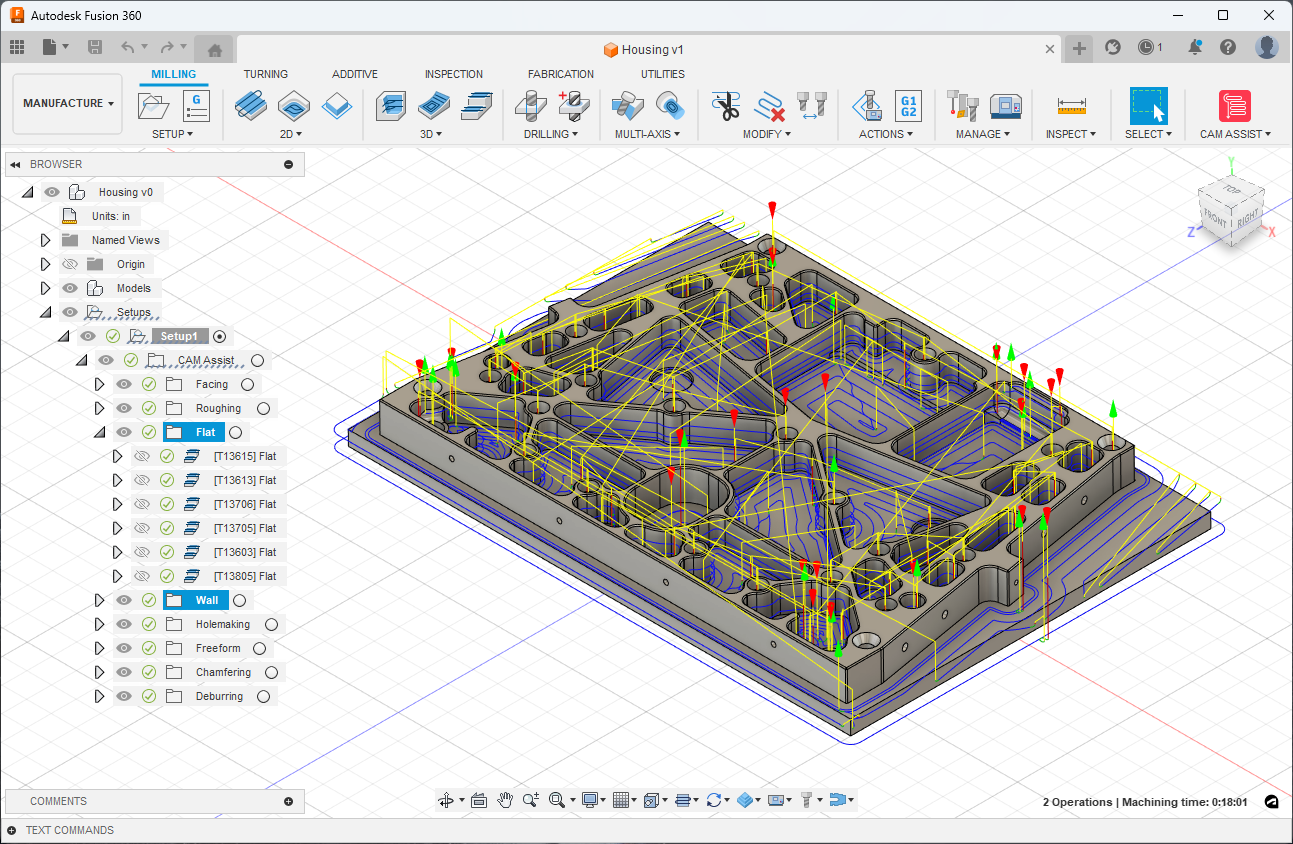
Since launch, we’ve had well over 250 parts loaded, and over 5000 toolpath operations generated. While we can’t give specifics (or even access specifics) around what the parts look like or how much time has been saved (due to GDPR and data protection), it’s incredibly gratifying seeing customers use the software in a live environment, and hearing the benefits they’ve witnessed.
Creating the software that works in a manufacturing environment, understanding principles of CAD and CAM required much more than just coding expertise. It required a deep understanding of the physical world and the intricate processes involved in precision machining. By operating our own facility, we have a dedicated space to test, refine and improve our software solutions - live.
What we've observed:
- Customer love the fact that they can load a complex part and use CAM Assist to save significant time on the majority of the programming and have a head start against their competitors
- Customers love the fact that different users are able to have consistency with the way parts are created. It now doesn’t matter that different staff may be running CAM Assist - the output is exactly the same!
- One customer mentioned that “different programmers have their own style which makes it hard to replicate when they leave, we need to modify their programmes and it’s difficult to get consistent results”. CAM assist has successfully enabled standardisation across the machine shop.
- One machine shop manager mentioned that CAM Assist can help “ease CAM bottleneck”. This is because CAM demand is not consistent - you’re either overstaffed or understaffed. This has a knock-on effect on your entire process. Your machines can’t run themselves, and CNC machine downtime means lack of sales, longer lead times and inefficient programming. If you’re unlucky - this leads to wastage due to scrapping parts that just aren’t fit for purpose. Not very sustainable manufacturing!
- We’ve had lots of customers say they’ll be able to reduce the ‘expense of extra CAM seats due to CAM Assist”. Not only are they able to train their staff in a consistent and cost-efficient way, but they’re also able to “stop programming with G-code at the machine”. The reduction means that more parts are pre-programmed and the CNC machine isn’t idle as it waits for the G-code to be entered.
In a similar way, my last blog referred to being able to quickly prototype and iterate. One of our customers mentioned that they were able to now “make a sample part at the time of estimate and check cycle time. Validate test parts and avoid costly estimation errors”.
What would you do if you could save hours on your programming?
If you want to experience CAM Assist - test it for yourself! We can get you started with our limited time 14 day trial offer!