Supercharge machine uptime overnight
CAM Assist can be set up same-day and saves the typical workshop >1000 hours a year
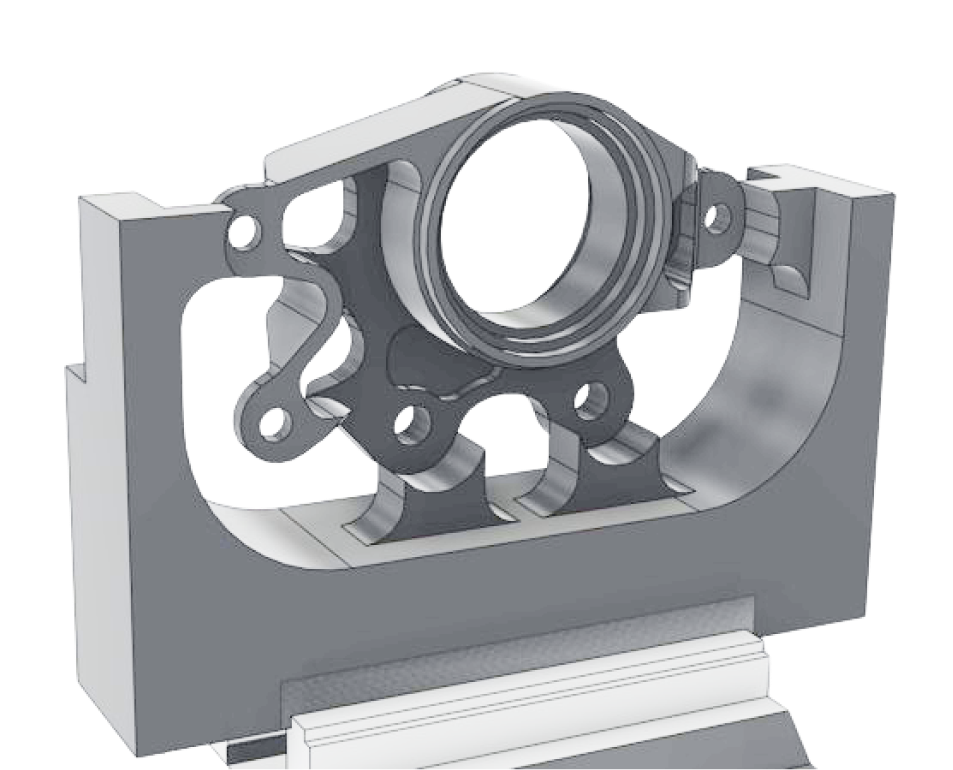
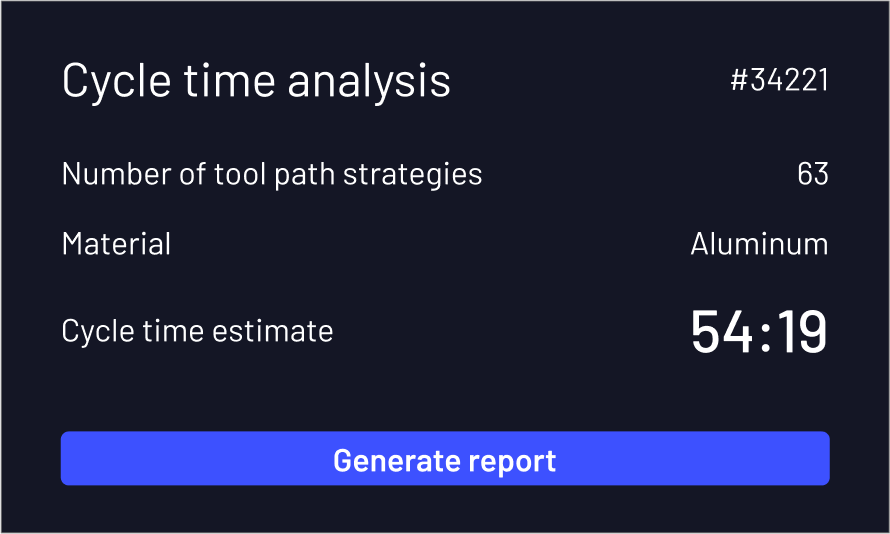
Win more business
Process >4x more quotes with cycle times estimates from an AI that understands your specific toolsets and machines
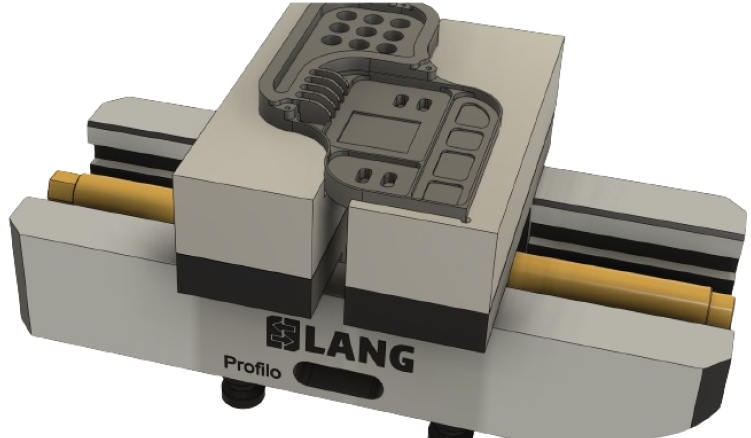
Design fixtures instantly
Generate custom soft jaw designs in seconds, cutting 40 minutes from CAD to first cut on average and freeing up your programmers to make more parts
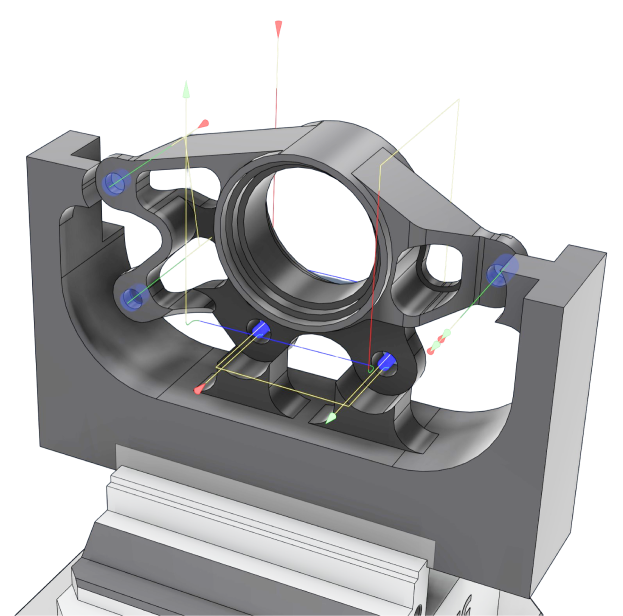
Remove CAM bottlenecks
Take your CAM programmers to 80% program completion at the click of a button, multiplying their productivity
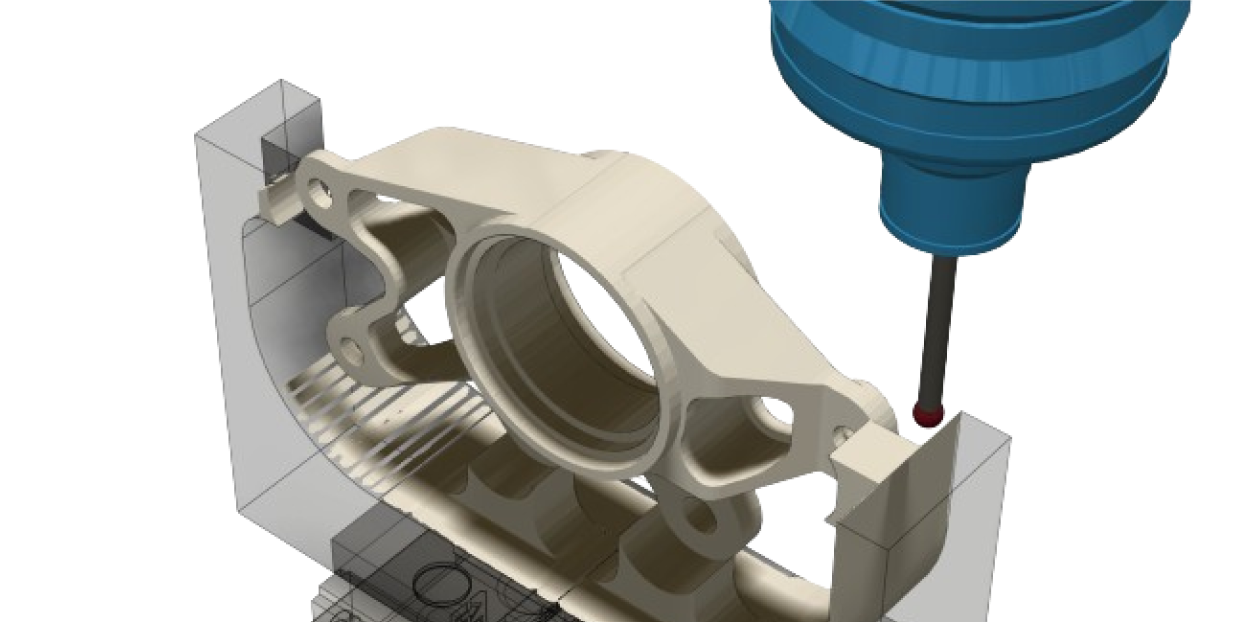
Increase right-first-time
Eliminate scrap caused by unreliable feeds & speeds with AI generated cutting parameters, tailored for every unique operation, tool and machine combination
Scale up production without scaling headcount
Difficulty hiring skilled labour is the #1 reported pain point in machine shops worldwide, and this is getting worse every year
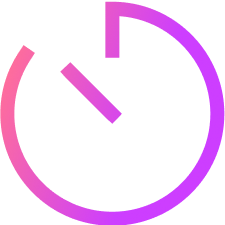
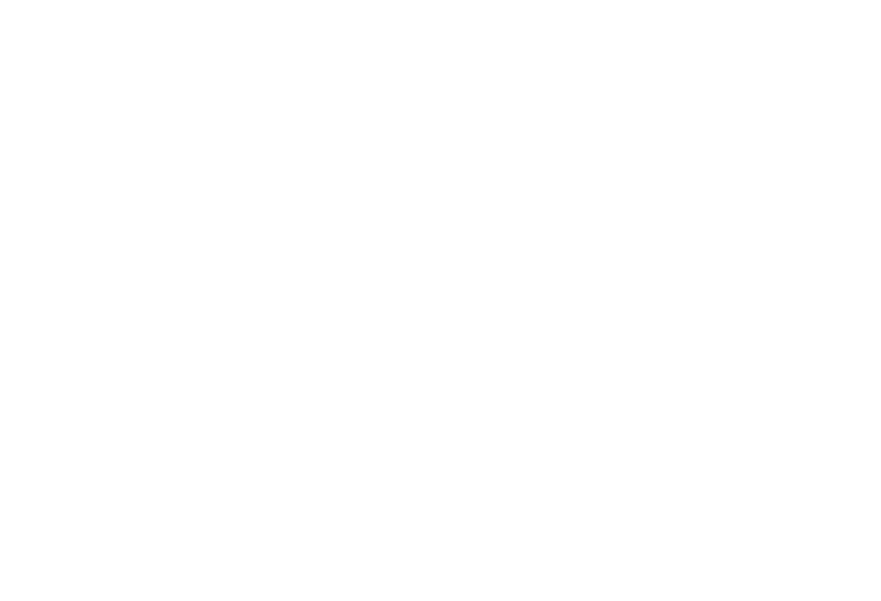
Win more contracts with AI cycle time estimation
Estimation is the hardest task to delegate in a machine shop, often falling to the owner. CAM assist reduces this burden and has been measured to >4x estimation output.
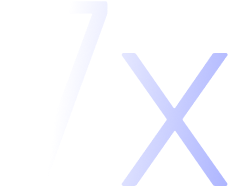
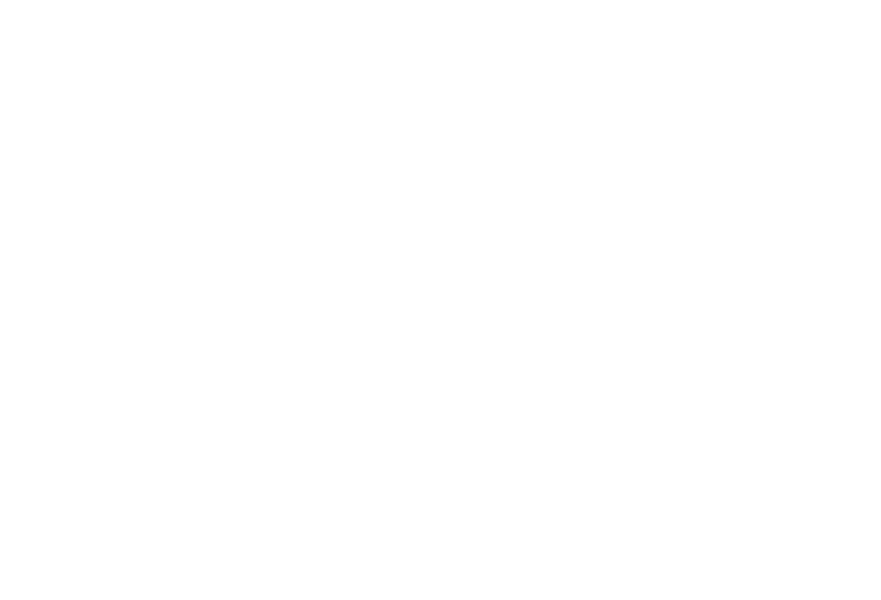
Never let unfinished CAM block a machine again
CAM Assist has been measured to reduce time from CAD to component by 7x on average, allowing programmers to make up to 7x more programs per day.
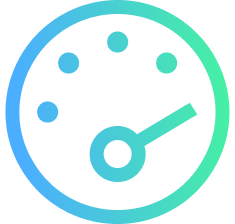
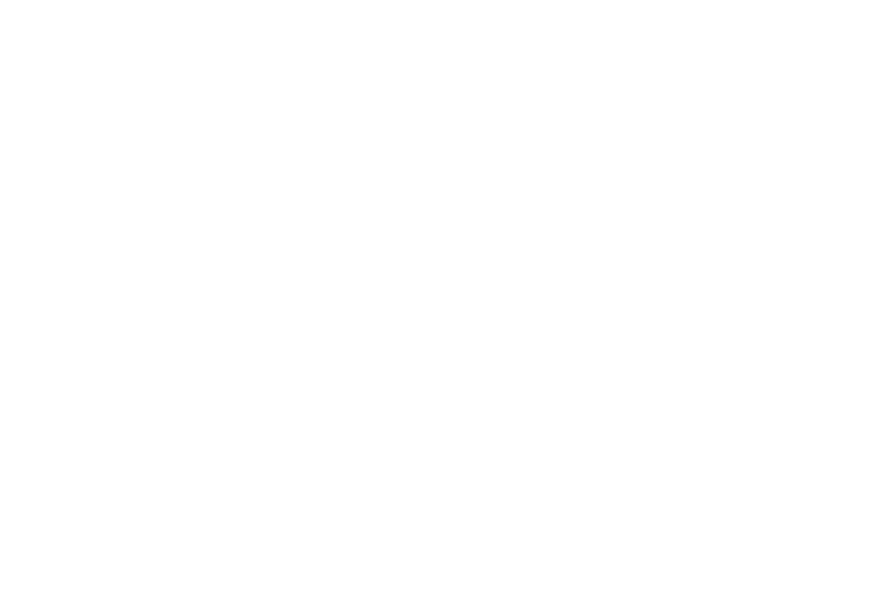
Multiply the productivity of your existing team
Difficulty hiring skilled employees is the #1 reported blocker to growth by machine shop owners. CAM Assist raises the output of your existing machinists.
Drive up OEE with the next generation of machining software
CAM Assist
Traditional CAM
Feature-Based-Machining
Don’t take our word for it
Hear directly from shop owners and machining experts.
FAQs
CAM Assist has a deep understanding of the rules and physics of machining, paired with the ability to generate trillions of possible ways to manufacture a component. It does this bearing in mind your unique combination of part + fixture + tooling + machine.
It rapidly simulates these possibilities, narrowing down the options to a sensible set of operations that will successfully produce the part to tolerance, which it then inputs this directly into to your CAM package, much in the same way you would. This leaves you with a CAM program that is ready to simulate and edit.
CAM Assist will rarely provide a perfect strategy first time, but it will usually get you 80% of the way there - it is up to you to decide how to use that time.
Whereas feature-based machining can identify a certain feature on a part and enable you to make a macro for that feature, CAM Assist is an AI that’s been programmed to know how to make the whole component.
That means instead of recognising features and drawing from a template library you have built, CAM Assist works out the best toolpaths and strategies based on all the elements that a component consists of, because CAM Assist understands the part holistically, as a whole.
CAM Assist is an AI that understands the physics and rules of CNC machining, works at full effectiveness out of the box, and receives new capabilities added monthly enabling it to program more components with faster cycle times and better process robustness.
By contrast Feature Based Machining is not AI and does not understand CNC machining. It can take upwards of a year to build an effective macro database, and most factories employing Feature Based Machining also employ full-time technicians to continually expand this database.
Feature Based Machining is known for being inflexible and difficult to set up. It tends to be most popular in major manufacturing operations producing large families of similar components - a use case in which it excels. It is rarely found in the subcontract machining arena.
CAM Assist requires no setup and little training, integrating directly into your existing CAM package. It also contains powerful additional capabilities including instant cycle time estimation, instant fixture generation and instant feed and speed optimisation.
Yes we offer a 14-day money back guarantee.
CAM Assist is purchased on a per seat basis and attaches to your CAM seat license. Our fair usage policy requires that you purchase a seat for every active user.
CAM Assist works with almost every CNC milling machine.
It will pull your machine parameters directly from your CAM package, and if you do not have machines already defined you will need to provide for each machine the minimum and maximum spindle speed (RPM), maximum spindle torque (Nm), maximum spindle power (kW) and maximum table feed (mm/min).
CAM Assist does not currently support other types of CNC machine such as lathes and mill-turns, though this is in development.
We use AWS cloud as our provider. Data is stored and processed in alignment with GDPR. If you have any further questions on this please contact camassist@cloudnc.com.
Head over to our Youtube channel here. We have an ever evolving library of video tutorials to assist you with anything from 3+2 axis maching to setting up and configuring your tool library.
If you haven’t already, follow this link to get a demo of CAM Assist from one of our team. Their experience in manufacturing will help us understand you challenges, and take the best-next steps from there.
No - CAM Assist works directly within your existing CAM package and therefore does not require new post-processors.
CAM Assist Cutting Parameters AI is the engine powering the feeds and speeds underlying the automatic machining strategy generation in CAM Assist. This dynamic physics model computes feeds and speeds based on the characteristics of the chosen machine, tooling, materials and numerous other parameters. With the Cutting Parameters Explorer tool, users can also modify these parameters dynamically for each toolpath operation to account for the specific factors of the job at hand.
.png)