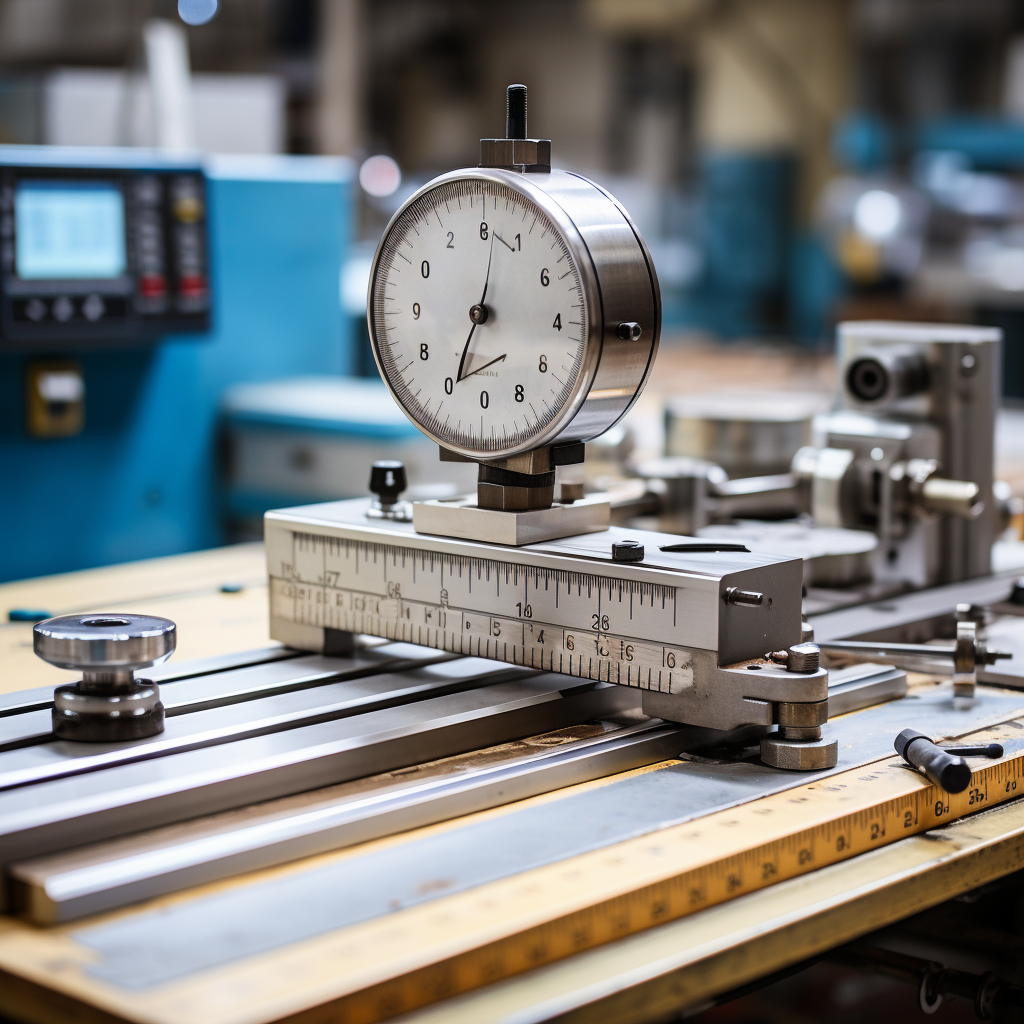
Consistency of process: the key to excellence in precision machining
Precision machining is a cornerstone of modern manufacturing, transforming raw materials into meticulously crafted parts and components that find use in virtually every industry – from aerospace to energy, and from automotive to consumer electronics.
At the heart of a successful precision machining operation lies an often-underemphasised element: consistency of process. Why is consistency important? Let’s dive in.
1. Assurance of quality
The essence of precision machining is, as the name suggests, precision. Whether it's a surgical instrument, an aerospace component, or any other critical part, there's a slim margin for error. A consistent process ensures that every single item produced meets the exacting standards required.
2. Economies of scale and cost efficiency
When you've established a consistent machining process, scaling becomes more straightforward. You can produce large quantities without compromising on quality, ensuring that production costs remain stable and predictable. Inconsistencies can introduce unexpected costs, from rework to scrapping materials, impacting the bottom line significantly.
3. Predictable timelines
Consistency in process means predictability in outcomes. This predictability allows manufacturers to give their clients accurate delivery timelines. In industries like aerospace or automotive, where supply chain dynamics are intricately timed, this is a priceless advantage.
4. Reduced rework and waste
A consistent process minimises errors. Fewer errors mean less rework, which in turn reduces waste in materials and time. This not only results in cost savings, but also contributes to more sustainable operations.
5. Enhancing machine life
Machinery, especially the advanced CNC machines employed in precision machining, represents a significant investment. A consistent process means that these machines work under predictable conditions. This predictability, when maintained within optimal parameters, can prolong the lifespan of the machinery and reduce the frequency of costly repairs or replacements.
6. Skill development and training
A defined and consistent process provides a stable platform for training new employees. When every aspect of the process is standardised, it becomes easier to train, evaluate, and improve. This promotes skill development within the workforce, ensuring that every operator reaches a high level of proficiency.
7. Continuous improvement
Consistency doesn’t mean stagnation. A consistent process is a benchmark, a standard from which one can measure deviations and seek improvements. As technologies evolve and methods improve, having a stable starting point makes it easier to integrate new advancements systematically.
8. Client trust and brand reputation
In the world of manufacturing, reputation is paramount. A consistent process leads to consistently high-quality products. When clients know what to expect and are seldom, if ever, disappointed, trust is built. This trust can translate into long-term partnerships, repeat business, and a strong market reputation.
So, consistency in precision machining is more than just a best practice—it's an imperative. It underpins quality, efficiency, trust, and growth. As technology continues to evolve, introducing newer methods and tools, the emphasis on process consistency will remain unwavering. After all, in a domain defined by precision, there's no room for uncertainty.
At CloudNC, our CAM Assist solution helps manufacturers be more consistent with their CAM programming, by standardising tool strategies between programmers and reducing variance. If you think our solutions could potentially help you, get in touch and benefit from the very latest in manufacturing technology, today!