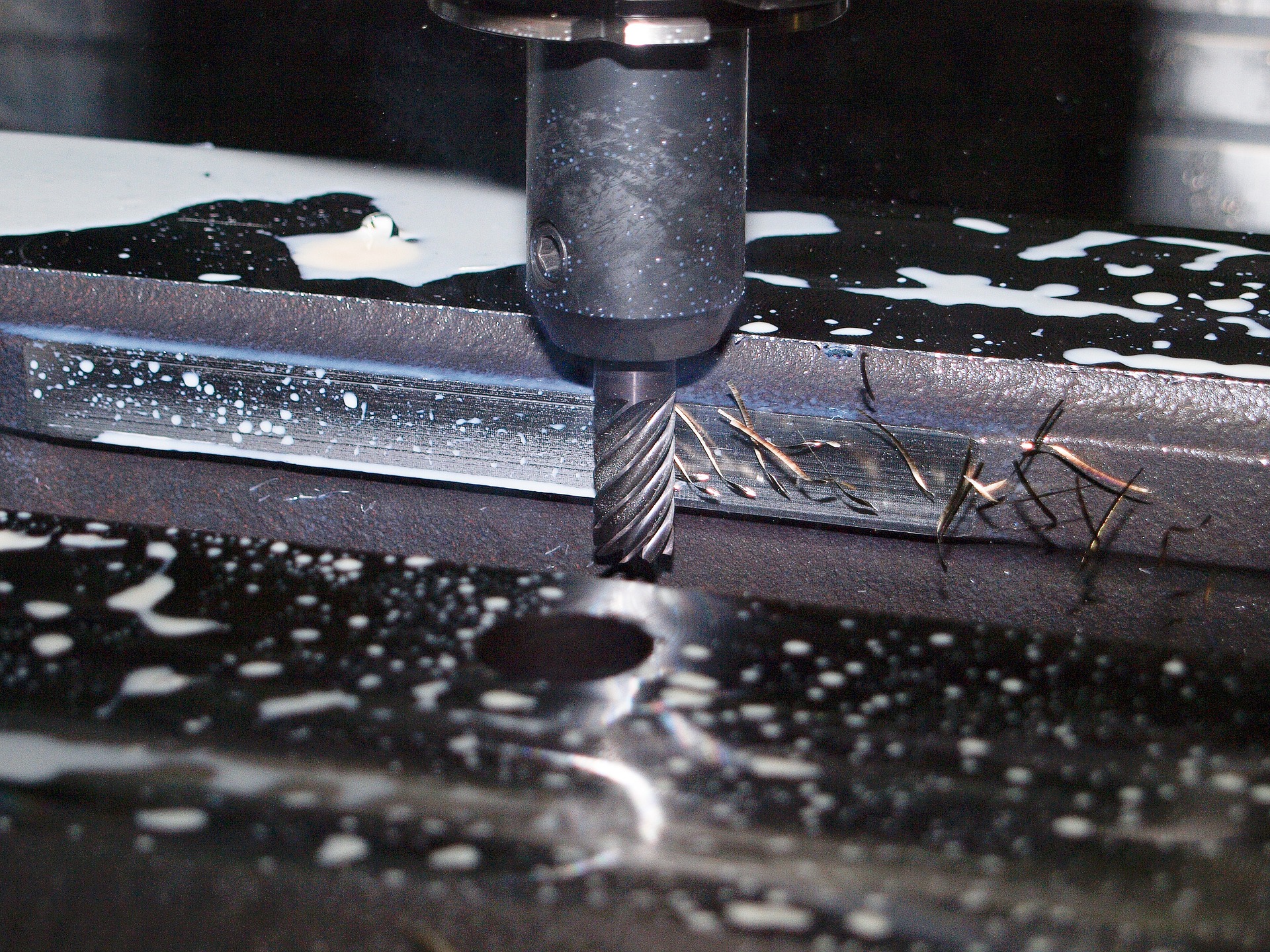
CloudNC as a company exists to make precision manufacturing more accessible and efficient than it is today. We want to use software to remove the obstacles that prevent anyone from being able to make new components easily - ideally, one day, in a single click.
That’s the mission - and if we can pull it off, we’ll revitalise the manufacturing industry worldwide, shorten supply chains and enable corporations to be able to make components reliably and quickly, close to home: resulting in wins for everyone.
But there’s an unspoken question in the above - why does precision manufacturing need to be improved in the first place? And why haven’t incumbents been able to enact the positive changes required to make the sector run more smoothly?
Well, it’s all down to scalability - as we’ve found out, in part, through operating our own factory in the UK. Here’s a quick dive into what the problems in precision manufacturing really are, and why they are so difficult to fix.
Problem 1: it’s all manual
The first element that makes precision machining hard is that every job is different.
Every time a customer asks you to quote on how much it would cost you to make a new component for them, it’s for a product that you’ve never seen before. And that means you don’t know how to make it, or how long it will take, or exactly how to meet the lead times or quality requirements.
As a result, it’s incredibly difficult to get the quote right, and there’s no manual to help you get there. Estimate too low, and you’ll undercut the market and win the order, but end up losing money on every part you make. Too high, and you won’t win the order. There’s a sweet spot in the middle where you can both win the order and make money, but it’s difficult to get to that spot as there’s no process for finding it other than having knowhow, based on years of experience. Get it wrong consistently, and your workshop will fail.
Consequently, for quoting, you often end up relying on a single guru within the business, usually with 30 or so years of experience, who basically estimates, hopefully accurately, on what the price point is. This person is therefore absolutely critical to a manufacturing business, and it’s extremely difficult to replicate their experience and know-how and share it with colleagues, as it’s all located in their head.
Exacerbating the problem is that even if you have a person with that kind of experience, it’s all specialised and localised to one specific factory - to the extent that if you dropped them into a new facility and asked them to do their thing, they’d struggle. Every factory has a different cost base, different machines, specialities and quirks, so the correct quote that would make a lot of money for one factory would end up with you losing it at another.
Problem 2: timing
Just as difficult as quoting for a job, is scheduling the job once you have it. During the quoting process, your expert has guessed how long everything is going to take in a perfect world - but you don’t actually know how long it will actually take until you start making your parts.
That’s problematic, as if you discover that you need twice as long, then you’re late on delivering that part which makes you late on any other jobs you have on too. Even then, you can’t change the price you’ve quoted to the customer.
Compounding the problem is the manual nature of scheduling in factories. I’ve personally spoken to companies with hundreds of CNC machines, who still schedule all the work that they’re expected to do using Microsoft Excel. Smaller companies with fewer machines are often using a whiteboard.
So the challenges of scheduling work accurately mean you’re already in a garbage in, garbage out kind of situation at your factory in terms of timing - and that problem is exacerbated again by all the variables that mess up your timing even further.
Problem 3: variance
To start with, there’s a trillion ways of programming every new component, and everyone will do it differently, based on their own expertise.
Then you can mix in more variables. Programmers have their favourite tools that they prefer to use, and their favourite toolpaths. Tools can behave perfectly the first 50 times you make a component, but on the 51st, perhaps your tool chatters in a particular corner and wears out quicker than expected, broke and failed to clear an area out properly, and then the next 15 tools in the process all hit material that wasn’t supposed to be there and snap too. In an environment where one wrong move sends your spindle at high speed into another solid piece of metal, you’ve now got an expensive broken CNC machine.
And what are you trying to produce, in the midst of all this chaos? A component that might need to be accurate to within thousandths of a millimeter, or even a sub-micron: the kind of tolerance where the slightest change (such as the thickness of concrete on your shop floor, whether the sun has come out and is heating one side of your machine through the window, or if your operator crashed the spindle lightly on a previous run and hasn’t mentioned it yet) can create inaccuracies that take you out of that narrow tolerance band
All of these factors mean that the safest course for factories is to make their lives as simple as possible: remove the variance as much as possible, and specialise on one thing. You want to get to a situation where you’re working in a specific industry (say, oil and gas), making the same parts for the same three or four companies, so your business becomes predictable and you don’t need to re-invent the machining wheel every day.
Economically, that makes sense: but strategically, it means your factory ends up being tied to a small number of potential customers, with little natural defence if the prevailing market winds change and your purchasers decide to go in a different direction. After all, what if you’re an aerospace machining specialist and COVID grounds the world’s fleet?
Tipping the balance
So, how do you cope with all these challenges?
Unfortunately, the answer is experience. People who’ve been in this industry a long time are really, really good at their jobs. They’ve seen enough to be able to predict a lot of these problems and intercept them before they happen - whether that’s to realise that a new truckload of metal is behaving differently from usual, to seeing the challenges that a scheduled quote provides before work starts.
Why “unfortunately”? Well, because:
- It’s incredibly hard to find people with this expertise in the first place - it takes years and years of hard work to develop
- When you’ve found these people, you can’t scale them or share their knowledge easily with others - so they aren’t replicable
- It’s disappearing: these people are retiring from the industry, and not being replaced
Add that all together, and you have a situation that can’t be fixed within the industry itself - you need to look outwards, for a solution that looks at the problem in an entirely different way.
Fortunately, that’s where our CAM Assist software solution comes in… as it accelerates and autocompletes much of the programming process for CNC machines, removing many of the variables when it comes to machining a part, as well as effectively putting experience directly in the hands of new machinists, helping to fill the skills gap.
You can see our CAM Assist software in action here - but if you want to get your hands on it today, sign up to our free trial now!